Nudura Insulated Concrete Forms (ICF's) are gaining popularity as an alternative building material.
Nudura ICFs offer a host of benefits, such as faster construction times, lower insurance rates, and quieter interiors, but the two primary reasons behind their growth is their remarkable durability and energy efficiency.
ICF's allow owners to create a building that is more comfortable to be in while only using half the energy to heat and cool as regular construction. ICF walls protect occupants and their belongings from tornadoes, hurricanes, wildfires and other disasters. From a design standpoint, ICF technology is extremely flexible; the architecture can match virtually any style, and ICF's are compatible with all popular interior and exterior finishes. And yet the cost of ICF constructions is typically less than 5% more than wood. When the monthly expenses of living in an ICF house are considered, there is typically a net gain of monthly budget. The same holds true for commercial buildings. Many churches, schools, stores, and hotels have found that ICF's allowed them to build a better structure for far less than expected.
The key to all these remarkable attributes is the combination of expanded polystyrene (EPS) foam panels and reinforced concrete. The concrete provides exceptional strength and thermal mass; the EPS provides a continuous layer of the world’s best insulation, and is an ideal substrate for many finishes.
Energy Efficiency:
The actual, real-world performance of an ICF wall far exceeds its nominal insulation value. This is due to a combination of three factors: more insulation, less air infiltration, and high-mass walls.
Higher Rated, Continuous R-Values:
EPS foam, from which ICF's are made, is one of the best insulating materials yet invented. The R in “R-Value” stands for thermal resistance, and the higher the R-Value the better the wall is at stopping the flow of heat.
Homes built using wood frame construction typically have exterior walls rated between R-13 and R-19. ICF walls, on the other hand, have foam with tested insulation values of R-24. (A frame wall would need to be a full 12 inches thick to achieve a similar rating!) With the option of adding additional foam inserts R-values of R-47 can be achieved.
ICF's offer continuous insulation, so there are no gaps in the wall assembly with a lesser R-value . With frame construction, the average frame wall is 25% wood, so even though the fiberglass or cellulose may be rated as R-13 (for 2x4) or R-19 (for 2x6), the ‘whole wall’ insulation value is significantly less. The actual R value for a 2x4 is R-4.4 and R-6.8 for a 2x6 stud. So if you look at the whole wall make up, 25% of a 2x4 wall is actually R-4.4 if you add this to the 75% of the wall that is R-13 then the end result is a wall assembly that is actually R-8.74. Using these same calculations a 2x6 wall is actually R-13.11.
With Nudura ICFs the owner is assured of continuous insulation without gaps or installation mistakes.
Airtight Construction:
Anyone who has lived in a drafty house when a winter storm howls outside knows how significantly air infiltration can affect insulation value. For the past decade or so, home builders have tried to address this by covering exterior walls in a layer of paper-like “home wrap”. However, frame walls are made from dozens of individual components which guarantee that outside air will be able to infiltrate the living space.
ICF walls, though, are virtually airtight. Even hurricane-force winds can’t force their way through four to six inches of solid concrete.
Thermal Mass: 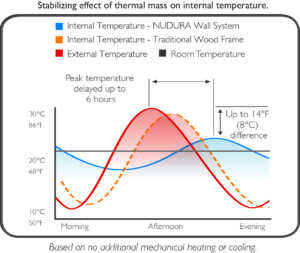
Many historic buildings in the American Southwest have pleasantly cool interiors even when the hot summer sun has been beating down on them for hours. The secret is in their adobe walls -usually several feet thick – that take hours to heat up. And when the sun sets and temperatures drop, the stored-up heat keeps the interior pleasant through much of the night. This phenomenon, called thermal lag or temperature damping, is due to the mass of the walls.
Like adobe, ICF walls take advantage of thermal mass. Even a modest ICF home uses dozens of yards of concrete, and that weight creates thermal lag in ICF structures, moderating temperature swings.
Disaster Resistance:
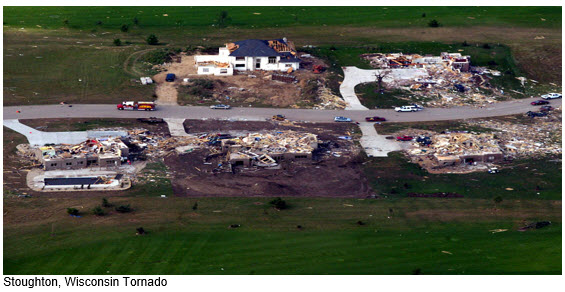
The monolithic structural concrete wall system enabled by ICFs is ten times stronger than a wood framed wall. As a result, an ICF wall system will withstand wind speeds of up to 250 miles per hour and will more than stand up to the positive and negative pressures from a tornado. An ICF wall will resist flying debris at 100 miles per hour. It resists seismic events because it has over six times the racking load resistance and it provides the stiffness and ductility required compared to wood frame alternatives.
An ICF wall system is non-combustible and has up to a four hour fire rating resisting temperatures of up to 2000°.
An ICF building may qualify for reduced homeowner’s insurance due to its resilience and resistance to fire and disasters of all kinds.
ICFs are so disaster resistant that the U.S. military conducted blast-resistance tests using 50-lb. charges of TNT. The results were impressive enough that they now frequently specify ICF construction for “force protection” requirements.
Sound Absorption:
Most ICFs with a six-inch concrete core have STC ratings of 50 to 55. Insulated 2x4 wood stud walls with 3 ½ inches of fiberglass batt are rated near 38. The difference between an STC rating of 38 and 50 may not seem like much, but the decibel scale is logarithmic, so 50 decibels is ten times as loud as 40 decibels. In real-world terms, only about one-quarter to one-eight as much sound penetrates as ICF wall when compared to wood frame.
Design Options:
Adapting a plan for ICFs typically starts with stretching the exterior walls outward a few inches to accommodate the thicker walls. Other architectural flourishes are actually easier with ICF. For instance, radius walls, which are difficult to build with frame of block construction, are simple. Long clear spans can be easily accommodated, because the walls can carry the loads and steel beams these deigns require.
While ICF walls look dramatically different from plywood-sheathed from construction, they’re actually easier to work with for most exterior finishes. The foam substrate is perfect for cement-based stucco or textured acrylic finishes. Brick, stone, and manufactured stone are also applied more easily to ICFs than frame, as no additional vapor barrier is needed (in most regions). Siding –vinyl, wood or cement board—are also popular. It’s as easy as fastening the material to the ICF furring strips, clearly marked on the outside of the forms.
Costs:
An ICF home is estimated to cost 3% to 5% more than frame building. That’s about $10,000 for a $250,000 house. Financed with a conventional 30-year loan at 5% that amounts to an additional $55 on the monthly mortgage. However, because the homeowner will be saving at least that much on energy bills, the actual monthly cash outlay is less. In other words, when energy costs are considered, it’s actually less expensive to live in a ICF house. All of the other benefits—like disaster-proof walls, quiet interiors, and less maintenance—are added bonuses at no extra cost.
When you buy products from Tri-State ICF you will receive the following services at no additional charge to you:
- Plan conversion to ICF if required
- Delivery to your job site
- Bracing
- On-site service